UK-based startup SteamJet Space Systems has been selected to provide the propulsion unit for an ambitious CubeSat mission part of Artemis II, NASA’s first crewed return to the Moon in over 50 years. Developed by South Korea’s NaraSpace, the CubeSat will be deployed into a highly elliptical orbit, where SteamJet’s water-based thruster will play a critical role in ensuring mission success.
“Our participation in a mission that is part of NASA’s Artemis II program is a major milestone for our team,” said Marco Pavan, CEO of SteamJet Space Systems. “This milestone validates our technology as both sustainable and capable of handling complex space environments. It’s proof that CubeSats and Small Satellites no longer need to compromise on performance to stay green and compact.”
The K-RadCube satellite will be deployed into a highly elliptical orbit, with an apogee of approximately 70,000 km and a critically low perigee that would cause the spacecraft to re-enter Earth’s atmosphere during its very first orbit. Traditionally, only chemical propulsion systems, with their high thrust and specific impulse, would have been capable of executing such rapid manoeuvres. Thanks to performance levels comparable to chemical systems, SteamJet’s thruster can deliver the same critical capability using water instead. The propulsion system will perform a continuous 12-hour burn shortly after deployment to raise the perigee to around 200 km, preventing atmospheric re-entry and enabling the satellite to carry out its scientific mission in Earth’s radiation belts. If successful, this manoeuvre will represent one of the longest single burns ever conducted in orbit by a water-based propulsion system, marking a new milestone in sustainable in-space propulsion.
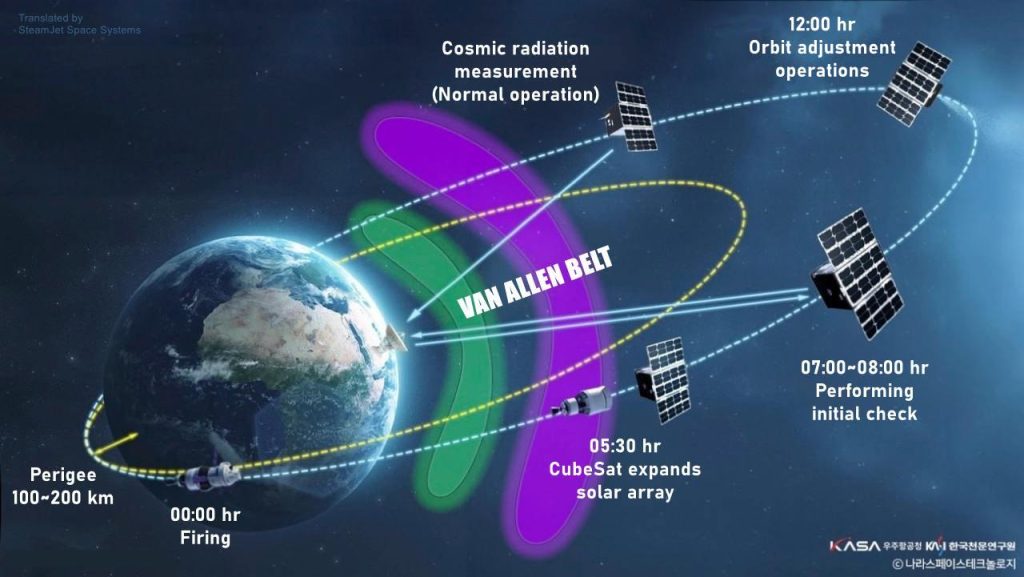
Critical objectives for the SteamJet thruster:
- Correct the perigee to around 200 km
- Orbit adjustment operation
- Extend the operational life of the CubeSat
This mission showcases how sustainable propulsion can now enable advanced orbital operations for CubeSats and Small Satellites without the need for toxic propellants. SteamJet’s system offers a safer, greener alternative while delivering performance previously limited only to chemical propulsion.
About SteamJet Space Systems
SteamJet Space Systems is a UK-based startup developing water-based propulsion systems for CubeSats and Small Satellites. Its proprietary steam-generation technology offers a green, safe, and sustainable alternative for in-space manoeuvres, enabling precise orbital control without the use of toxic or high-pressure propellants.
Detailed technical specifications, test data, and CAD models for the Steam Thruster One are available on the website. Discover how SteamJet innovations are shaping the future of sustainable satellite propulsion.