Today, many universities worldwide prepare the next generation of space engineers with a strong theoretical background. However, there is an obvious disconnect between academic education and hands-on experience, particularly in mission operations.
As a result, many aspiring engineers lack practical exposure to genuine real-world situations. The transition to space missions becomes more challenging and, in some cases, may lead to unnecessary risks.
The Challenge of Acquiring Practical Spaceflight Experience
In many cases, when students prepare to become astrodynamics specialists or satellite control operators, they mostly receive theoretical education through computer modeling and simulations. While those are an essential part of space education, they can only take students so far.
Many graduates enter the industry having never interacted with actual spacecraft propulsion or satellite propulsion systems in real-life conditions. They’re asked to contribute to high-stakes missions without having had the chance to test their skills – a gap that can lead to avoidable mistakes and steep learning curves.
Steam-based Thrusters Are Perfect for Education
SteamJet water propulsion thrusters are a natural fit for student satellite missions led by universities and research teams. They’re easy to work with, inherently safe, and designed to lower the barriers to real in-orbit learning — without the complications that come with traditional space propulsion systems.
Key Advantages:
- Water propulsion uses a non-toxic propellant, requiring no special certifications or hazardous protocols.
- Low-pressure operation makes it safe for classroom and lab environments.
- The satellite thruster mounts externally, preserving internal CubeSat volume for payloads.
- Simple electronics ensure quick integration with educational and research systems.
By incorporating SteamJet systems, universities enable students to engage directly with real spacecraft propulsion hardware — giving them an experience that goes far beyond simulation.
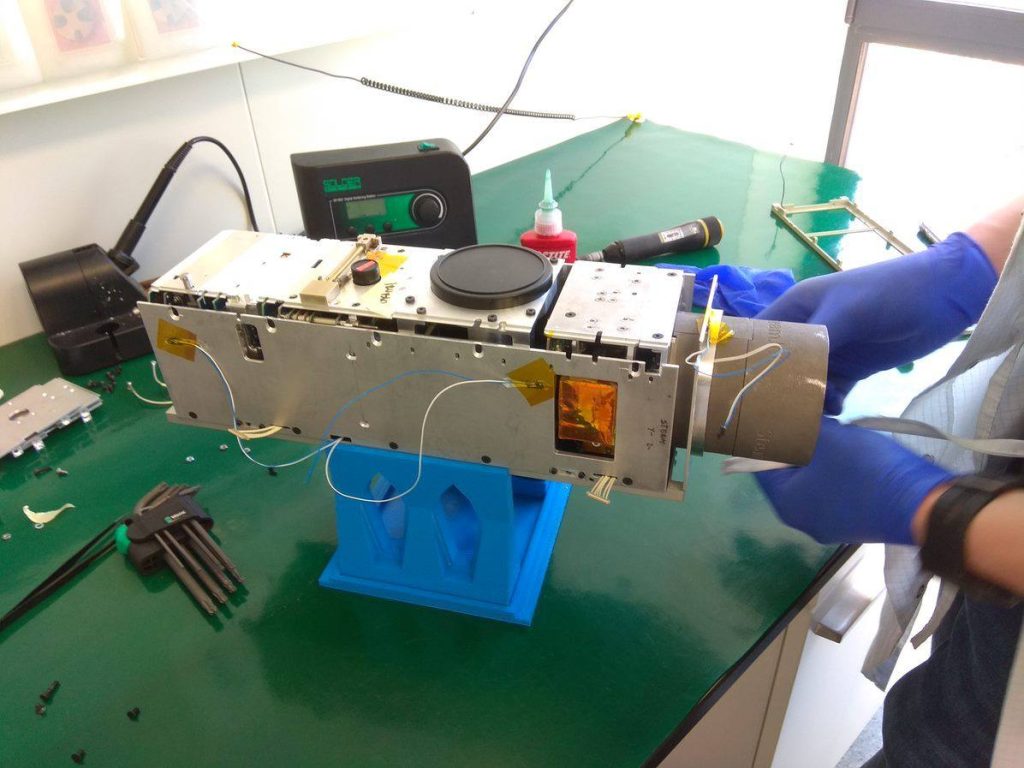
Applications in Academic Programs
1. Training the Next Generation of Satellite Control Operators
Future mission planners and satellite control operators can work directly with orbital dynamics and propulsion systems, building the critical skills required for satellite trajectory planning and spacecraft navigation.
2. Hands-On Experience with Spacecraft Propulsion
SteamJet systems allow students to practice orbital maneuvers and trajectory planning, helping them gain real experience in spacecraft propulsion control and mission execution.
3. Satellite Constellation Deployment
Student teams get the chance to manage satellite constellations, learning to coordinate cluster behavior and positioning.
4. Orbit Optimization
Educational missions are often launched as secondary payloads, hence they begin in suboptimal positions. CubeSat propulsion systems provide a chance for students to perform orbit adjustments.
5. Proximity Operations
Using CubeSat thruster units, students can simulate close-range maneuvers, alignment, and docking preparation.
Next Generation of Space Engineers
The next wave of space innovation depends on empowering students with more than theory. By giving them access to new space engines and operational space propulsion systems, academic institutions play a direct role in shaping mission-ready professionals.
SteamJet’s spacecraft propulsion technologies — including the Steam TunaCan Thruster and Steam Thruster One — offer a safe, effective foundation for experiential learning. These systems are specifically developed to support the growing needs of small satellite programs and to drive innovation in satellite propulsion across the academic landscape.
Ready to Bring In-Orbit Propulsion to Your Classroom?
Interested in integrating space propulsion training into your university’s program? We’re here to help. Contact SteamJet to learn how our technology can support your student satellite missions and help bridge the gap between theoretical education and practical, real-world spaceflight.
Detailed technical specifications, test data, and CAD models for our new space engines are available on our website. Steam TunaCan Thruster and Steam Thruster One. Discover how SteamJet innovations are shaping the future of sustainable satellite propulsion.